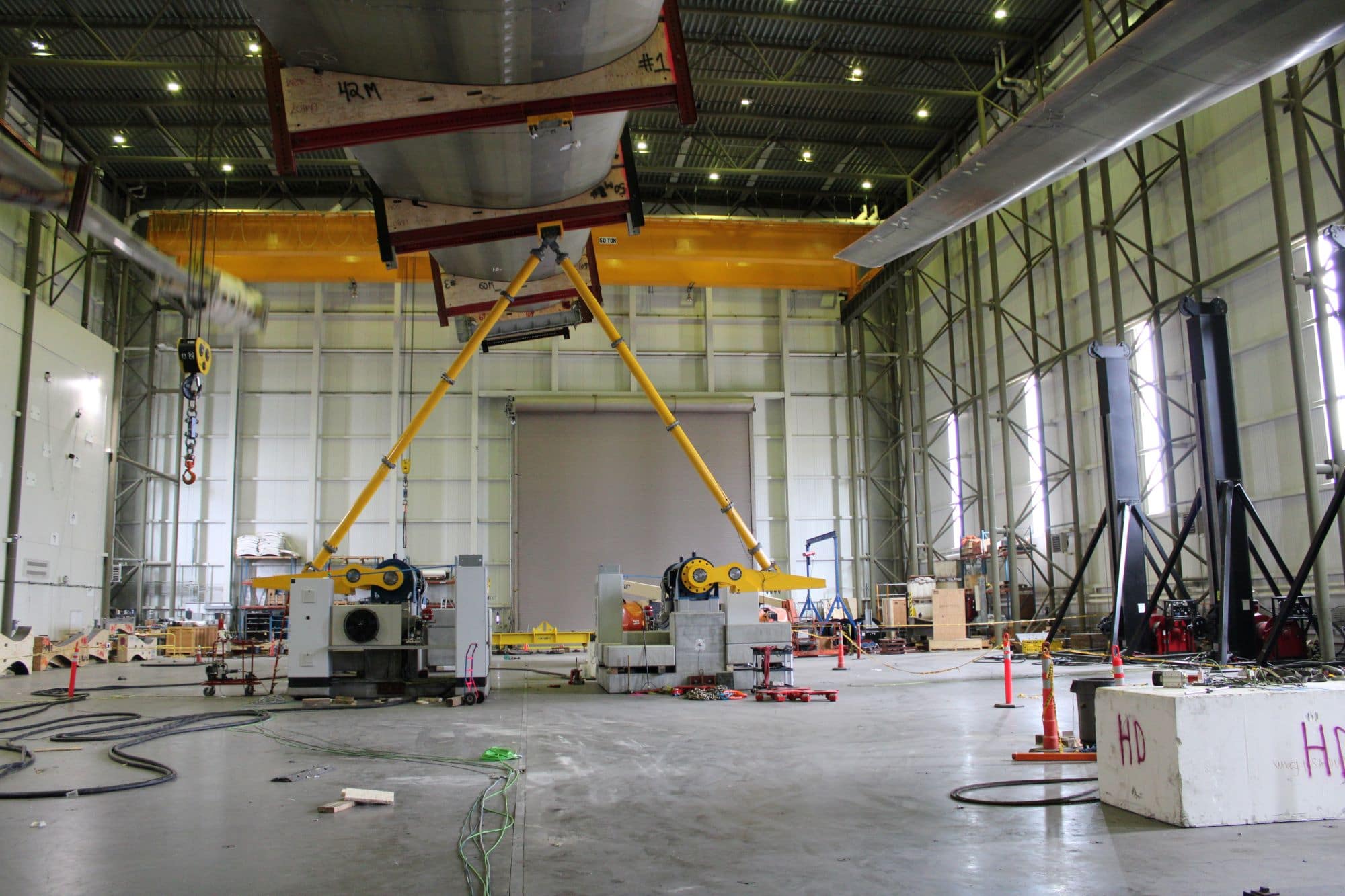
Test Systems
New test bench can test wind turbine blades up to 130 meters long
New test bench can test wind turbine blades up to 130 meters long
The development of new and larger wind turbines has never been faster than we currently experience. Hence, the rest of the supply chain needs to be ready and predict what the OEMs need next to keep up the development and limit the time-to-market.
To accommodate this, WTTC, that performs large wind turbine blade testing, ordered a new test bench with the size and power to test the next generations of wind turbine blades. This was part of the $4 million dollar US DOE and MassCEC’s grant to upgrade the blade testing equipment to accommodate the new and longer blades for the larger offshore turbine models.
With the new test bench from R&D Test Systems, WTTC has a future-proof test setup with the possibility to perform dual-axis testing, allowing more realistic test loads and results. The new full-scale multi-axis fatigue blade test system will also shorten the test time, as WTTC can use the same setup to test flap- and edge-wise fatigue test without changing the test setup.
Development of existing blade testing system
In 2021, R&D Test Systems built the first dual-axis blade exciter for the Danish Blade Test Centre A/S (Blaest). Since then, the R&D Test Systems has worked towards developing an even larger test bench for WTTC.
The new dual-axis exciter is approximately 40% larger in size and force and is able to apply 240 kN into the blade with an excitation power of 420 kW, enabling the test system to test blades up to 130 meters long.
“Delivering the first blade test setup in this size to the US is a milestone for R&D Test Systems. This is the first commercial dual-axis system that we have delivered. As American owned company by MTS and ITW it is a strategic goal to increase our US activities,” explains Key Account Manager Niels Pedersen from R&D Test Systems.
The blade exciter consists of two units that can deliver individual force and power up to 120kN and 210kW, respectively. The user-friendly software allows users to easily configure the test system for different tests. The two units can be used in combination for parallel or dual-axis operation or separately on other test areas.
Using the exciter units in dual-axis operation allows the OEMs to save valuable time when testing their blades. They can perform flap- and edge-wise fatigue tests using only one test system, saving changeover time when shifting between the tests. Furthermore, the multi-axial setup enables entirely new test scenarios that closely simulate what the blades are exposed to offshore.
“As a testing facility, we must be ready for what the OEMs will develop next. And with this test equipment, we will have the setup to meet the requirements, improve the testing quality, and simultaneously shorten the test time significantly,” says Rahul Yarala, Executive Director at WTTC.
After being assembled in Denmark, the test bench was shipped to Boston, US. During April, R&D Test Systems installed and commissioned the system on-site. After a successful commissioning, the test system was handed over to WTTC, which is already running the first test cycles with the blade exciter.
How can we help you?
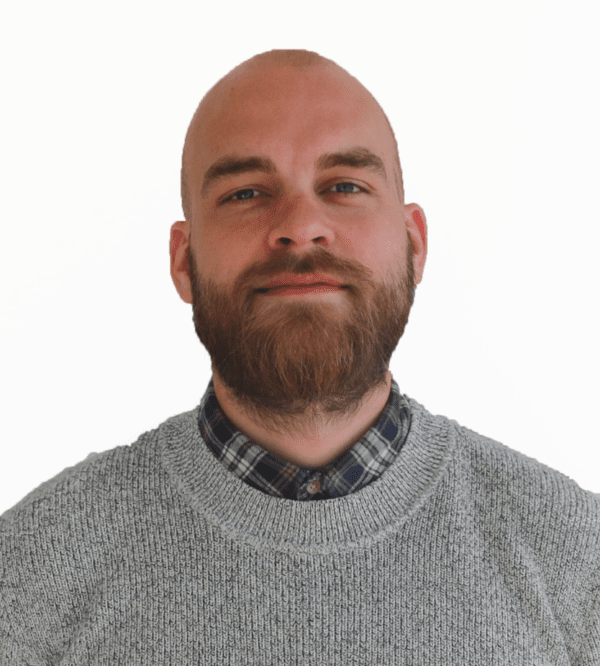