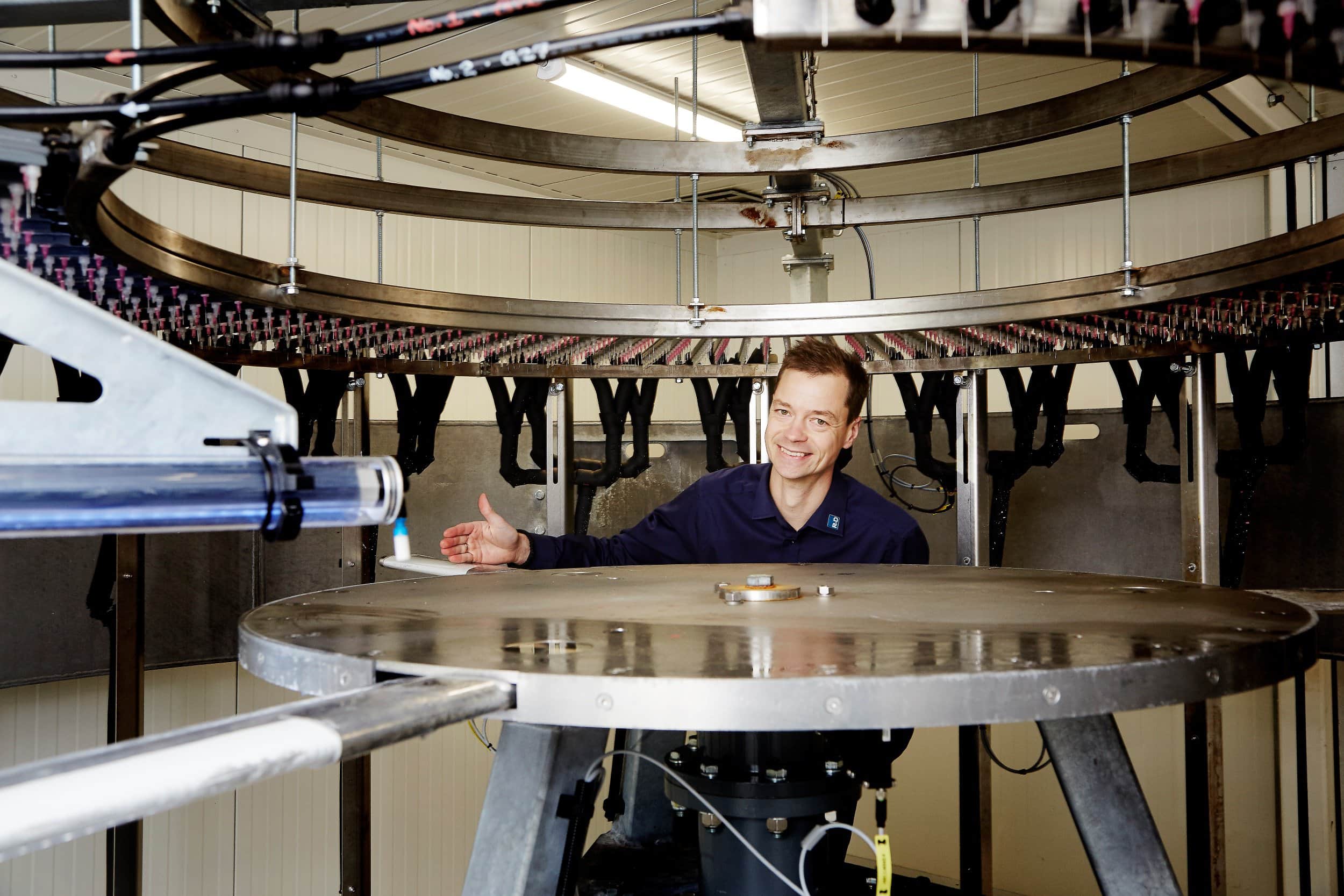
Test Systems
Danish company got unexpected success with a rain machine
Danish company got unexpected success with a rain machine
It is costly to replace a worn blade on an offshore wind turbine, and as more and more are set up at sea, the industry will increase its focus on durability. The specially developed coating must protect the blades from damage caused, especially by rain. Extensive testing is part of the product development, and the central role is played by a special rain erosion tester developed by Danish R&D Test Systems.
The company develops and builds, among others, tailored test benches that, in a few months, expose different wind turbine components to 20 years of wind and weather. The goal is to spot and fix the weak points in the construction before a new wind turbine model is sent for series production. No two test benches are alike, and at R&D Test Systems, they emphasize that they do not have finished products on the shelves. Every shipment is unique and specially designed.
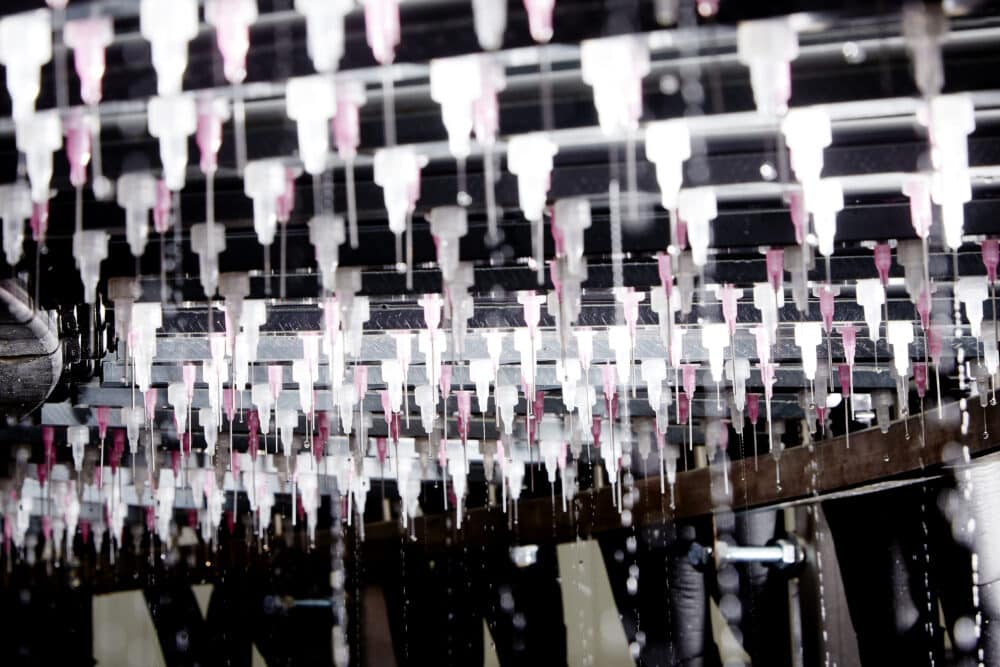
Unexpected success
With one exception. The company’s rain erosion tester has grown into a commercial success. Thirteen of its kind have been delivered, and a further three are being built, including a special powerful model ordered by DTU, who are world leaders in research on the erosion of wind turbines. R&D Test Systems also has its own tester stationed at the company’s headquarters in Søften near Aarhus, Denmark. It is rented out to customers and used by R&D Test Systems. The company uses it, among other things, for testing new types of aircraft wings developed under the EU project Clean Aviation Ultra Performing Wing led by Airbus, in which the company participates.
“In the industry, there is a huge interest in anything that can extend the lifetime of a wind turbine,” says Jesper Dal Hasager, Technical Product Manager at R&D Test Systems, responsible for what is internally referred to as RET (rain erosion tester).
“Within the last five years, people have realized its importance. The wind turbine effect is reduced, as well as the end-customer’s profit. Furthermore, it is enormously expensive when the blades break, especially on an offshore turbine. Ten years ago, you didn’t think much of it. Back then, the wind turbines weren’t that big, and there weren’t many. But now it has become a huge challenge,”
The first was customized
The first RET was built and sold in 2012. Still, in 2015, the development took a further step when LM Wind Power ordered a customized tester, developed with DTU and partly financed by the Energy Technology Development and Demonstration Program (EUDP). After this, new customers who could see the idea of investing in their own tester quickly arrived. It started to go even faster when they joined forces with DTU and DNV to establish a standard for coating tests based on the RET. The rest is history, now wind turbine and coating manufacturers and the aircraft industry use the machine to give the blade tips and edges optimal resistance.
Helicopter principle
As we all know, one raindrop does not harm, but many of them do. In the RET, they drip from 600 needles onto the test items. The machine is based on a three-bladed helicopter principle, and as needed, you can adjust the amount of rain, temperature, and speed.
“It has taken many engineering hours to develop a reliable and precise machine. The first tester was a particular challenge. It was before my time in the company, but I’ve heard that it was about to take off once,” laughs Jesper Dal Hasager.
“We have put many development hours into the machine to refine it, e.g., making the aerodynamic optimal so it does not interfere with the drops,”
According to Jesper Dal Hasager, the challenge is, among other things, that the humidity inside the machine comes very close to 100%. But since it must not be the humidity that wears out the blades, the tester is equipped with a ventilation system with a maximum capacity of 8,000 cubic meters of air per hour. In addition, the water used in the tester is purified. It is first sent through a softening facility that removes calcium, then through a reverse osmosis plant, and last, an ion exchanger so that it is finally as clean as possible and has a conductivity of less than ten μS/cm. Furthermore, the droplet size must be the same across the entire system of 600 needles with an average thickness of approx. 2.4 mm. With a heat pump, you can control the water temperature to thirty degrees and below, but not lower than four degrees, as it must be frost-free.
The tip is the most exposed
A wind turbine is most exposed to erosion at the blade's tip. Here, it runs the fastest, and it is also here that the most expensive, most resistant material is applied. To simulate the wear, the tester can run up to 173 m/sec. A special version of the tester was developed for the aviation industry and can run up to 224 m/s.
“You always test three identical subjects at a time,” explains Jesper Dal Hasager. “They must weigh the same down to a few grams; otherwise, the tester can’t run. Then, you program the test sequence and determine how many hours to test, the amount of water temperature, etc. Along the way, the tester slows down at fixed intervals for the camera to take pictures of the test subjects. Once the test is complete, the operator looks through the images and assesses how advanced the erosion is and exactly what defects can be seen.”
Used extensively
If it stands still for a long time, deposits form, and more and more of the 600 needles begin to block and need to be changed. However, there is not much downtime, neither on the R&D Test Systems’ rain erosion tester nor on the other testers at wind turbine-, aircraft-, and coating manufacturers. The testers that run the most have an uptime of 80%. With almost 16 RETs produced, one would think the market must be saturated. But Jesper Dal Hasager does not think so.
“We have sold it to serval industries, and it stands, e.g., in China and Japan. I think we can sell even more. For example, we have yet to sell one to the US market. In addition, we continuously develop the machine, and we are, e.g., looking at new types of cameras that can give us even better images. We are in the process of developing a software tool with machine learning that will be able to save the operator time when the images are analyzed. We’re not at all done yet.”
By Tech Relations for R&D Test Systems
How can we help you?
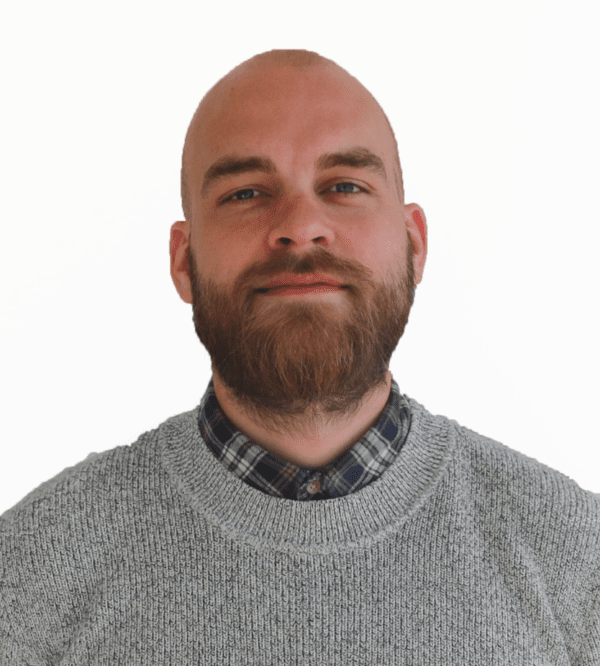