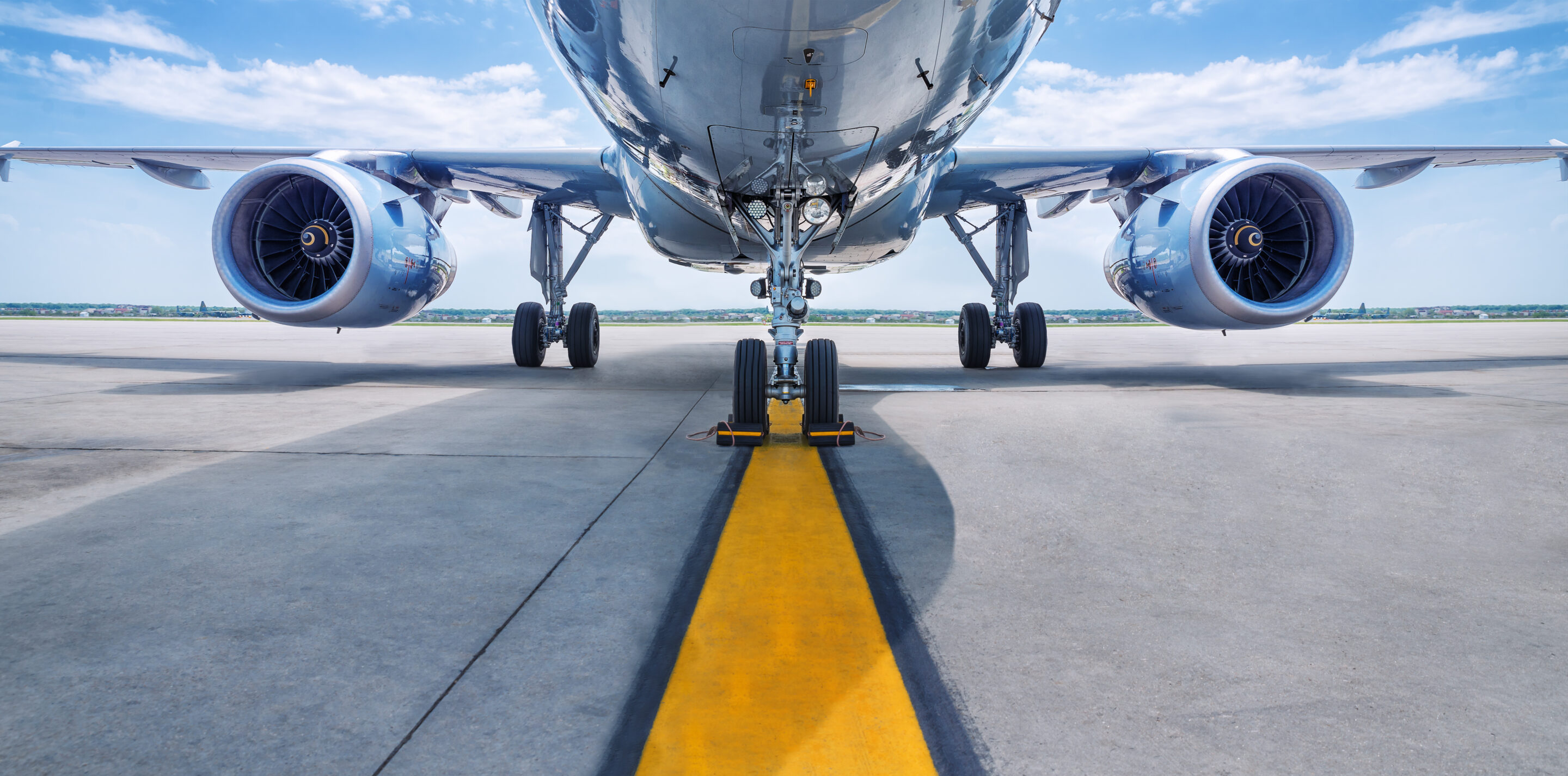
Case study
Behind the collaboration with Rolls-Royce
R&D Test Systems has developed, constructed, installed and commissioned a test rig for an aircraft engine power gearbox for Rolls-Royce.
This project was made in collaboration with R&D's American business partner MTS Systems Corporation. Both MTS and R&D have extensive experience with the development of test systems. The collaboration between the two companies and their respective skills were among the reasons as to why R&D was originally chosen as a supplier. With this delivery, R&D Test Systems has consolidated its position as a leading supplier of heavy-duty test systems.
Agile business partner
"Rolls-Royce was searching for an agile, competent, flexible and solution-oriented business partner with extensive experience within the development of test systems. This is one of the main reasons why they chose R&D," Peter Kattai Ulrikkeholm says, Business UNit Director at R&D. "We have worked directly with Rolls-Royce on this project and met on a regular basis for discussions and coordination."
Rolls-Royce was searching for an agile, competent, flexible and solution-oriented business partner with extensive experience within the development of test systems. This is one of the main reasons why they chose R&D.
Extensive documentation requirements
Rolls-Royce repeatedly visited R&D to discuss concept design, development and documentation requirements during the course of the project.
"Rolls-Royce is a very demanding business partner and their requirements to quality, documentation and the degree of detail are extremely high," Peter Kattai Ulrikkeholm says. "We have gained a lot of knowledge throughout the process and had an excellent foundation due to our many years of experience with the development of solutions for the industry. The feedback shows that we completed the job to perfection."
Many skills involved
It was primarily R&D's skills within the fields of project management, mechanical design, drive actuation systems, construction, documentation and installation, which were utilised in the process of developing the test bench.
Throughout the process, R&D has worked hard on optimising the design and ensuring that the test bench is sufficiently robust to withstand the test scenarios for which it will be used. 50 tons of specially designed steel has been used for manufacturing this test bench.
We have gained a lot of knowledge throughout the process and had an excellent foundation due to our many years of experience with the development of solutions for the industry. The feedback shows that we completed the job to perfection.
Well-established process
R&D worked for 24 months on the system delivery to Rolls-Royce. Halfway through the process, it became clear that the time schedule had to be accelerated by four months. This was achieved through ongoing consultation on prioritisations with the Rolls-Royce project team and the help of additional project engineers from R&D.
R&D was responsible for carrying out a comprehensive factory test of the test bench in Denmark and installing and commissioning the test bench at Rolls-Royce in Berlin. As a part of this process, R&D took great care to comply with the strict quality requirements and specifications which characterise Rolls Royce.
Tests have been completed
The tests on the test bench have now been carried out by R&D and specialists from Rolls-Royce. "Throughout the process, we have acquired valuable knowledge about the customer and the test bench, which means that we will be an ideal partner for the customer, when they carry out their tests and adjustments may be required," Peter Kattai Ulrikkeholm says. "In general, Rolls-Royce will be responsible for all future test work, and we will remain on the sidelines in case they need our knowledge and assistance."