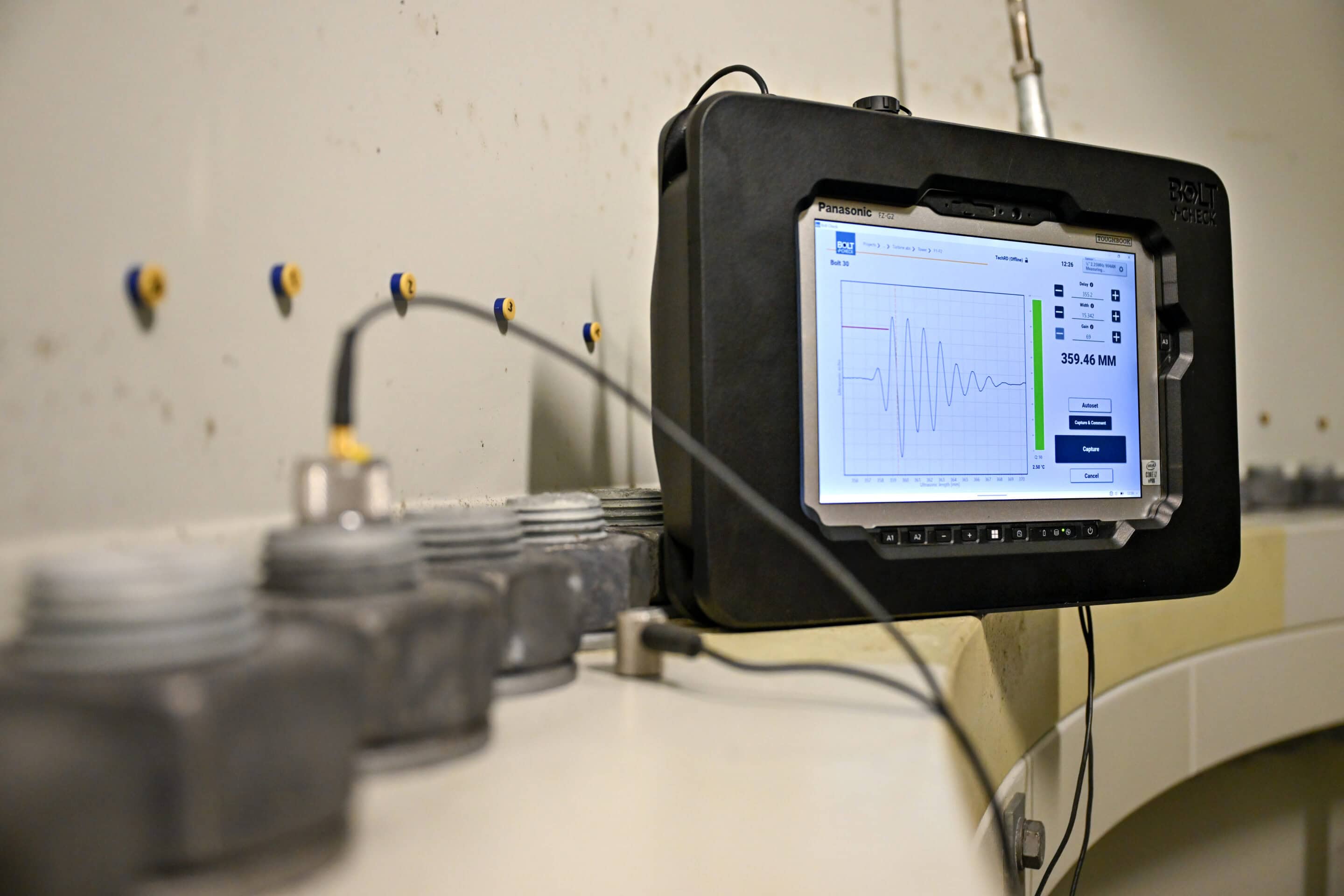
Bolt-Check
Bolt-Check: Accurate verification of bolted joints
Bolt-Check: Accurate verification of bolted joints
Easy, fast, and precise bolt verification
- Achieve precise bolt tightening accuracy
- Ensure full traceability with RFID-tagged bolts
- Reduce human error with automated data logging and reporting
- Lower maintenance costs with optimized, predictive service
- Lightweight device improves HSE and reduces physical strain
Ensure bolt reliability with ultrasonic verification
Bolt-Check is a state-of-the-art ultrasonic measurement device that allows fast and accurate inspections of bolted joints. Its intuitive user platform, ultrasonic technology, and traceability system let you instantly locate bolts in your database and appropriately schedule service and maintenance.
Bolt-Check is suitable for most bolt types and requires no special pre-treatment of the bolts. It can play an important part in maximizing operational time and minimizing failure. Bolt-Check provides a cloud solution with an intuitive bolt management database to store, sort, and examine measured bolts.
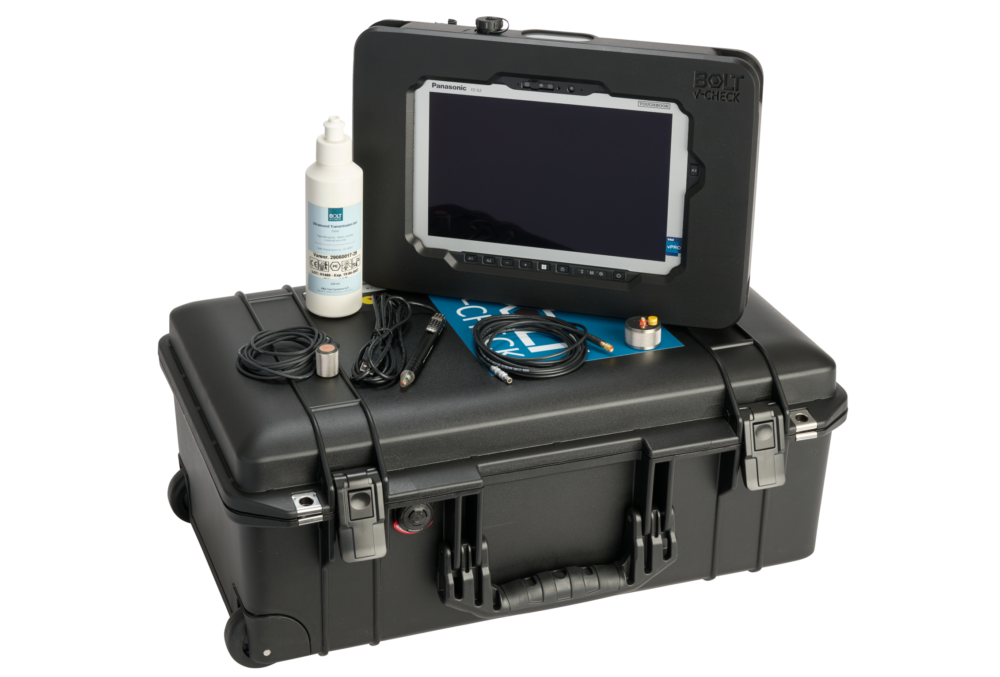
Easy and fast service of wind turbines
Get a closer view of how Bolt-Check with the Panasonic TOUGHBOOK works when servicing a wind turbine.
Ultrasonic measurement explained
Bolt-Check uses ultrasonic technology to accurately measure bolt elongation, a crucial indicator of whether the correct clamping force has been achieved. A small transducer sends a sound wave through the bolt and measures how long it takes for the echo to return. This return time reflects the bolt’s ultrasonic length.
By comparing the ultrasonic length before and after tightening, Bolt-Check determines the bolt’s elongation. To ensure accuracy, the system automatically compensates for temperature changes that affect both the bolt’s length and the speed of sound in the material.
Because ultrasonic length changes differently than physical length, Bolt-Check uses a built-in, material-specific stress factor to convert the data into true physical elongation. The result is a reliable, fast and non-destructive way to verify preload in bolted joints.
Traceability and cloud-based data management
A traceability tag equips each bolt with a unique ID, allowing full traceability throughout its lifecycle. Technicians can scan each bolt tag using Bolt-Check and the RFID pen to immediately access its measurement history and identification data.
All measurement data is automatically synced with the web app, a cloud-based platform for managing bolt projects, storing records, and sharing data. When connected to the internet, the Bolt-Check device continuously syncs with the web app to ensure all documentation is complete, organized, and instantly accessible from anywhere.
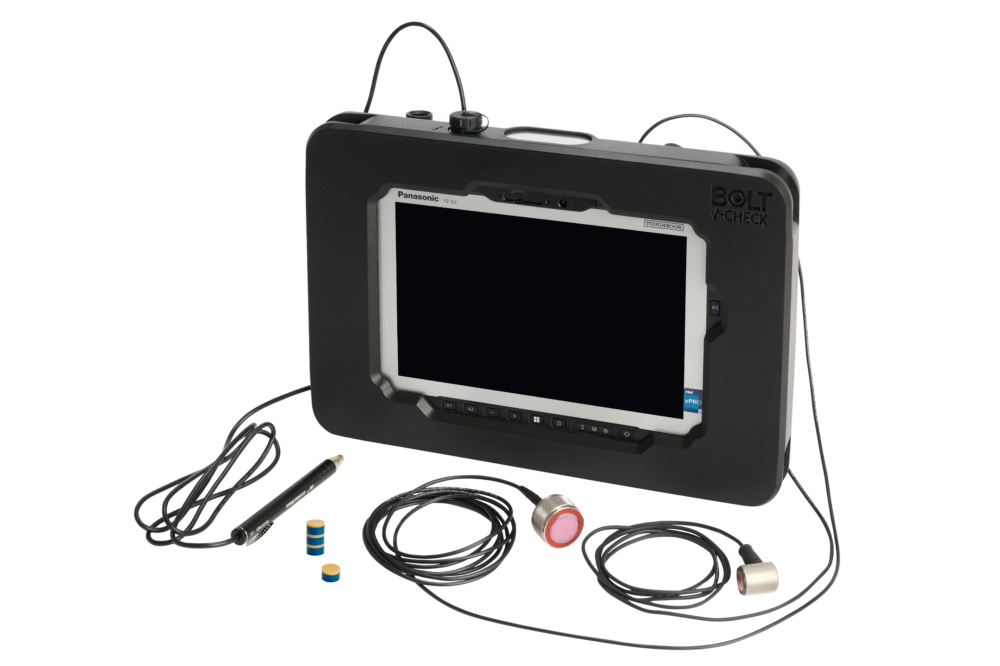
Other Bolt-Check services
Our team of specialists performs on-site measurements and reports about the condition of your connections.
Contact us for further information.
Test the relationship between applied torque and the resulting tension of bolts in our testing facility.
Contact us for further information.
Let’s solve your bolt tightening challenges
We offer deep technical insight, practical guidance, and solutions tailored to your specific needs.
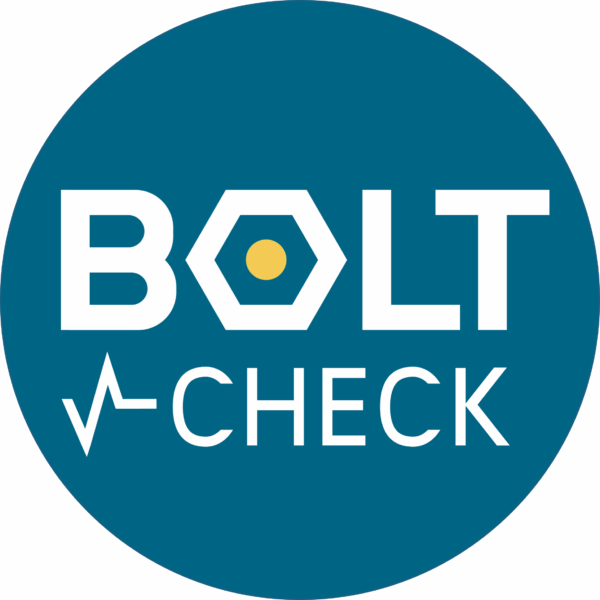