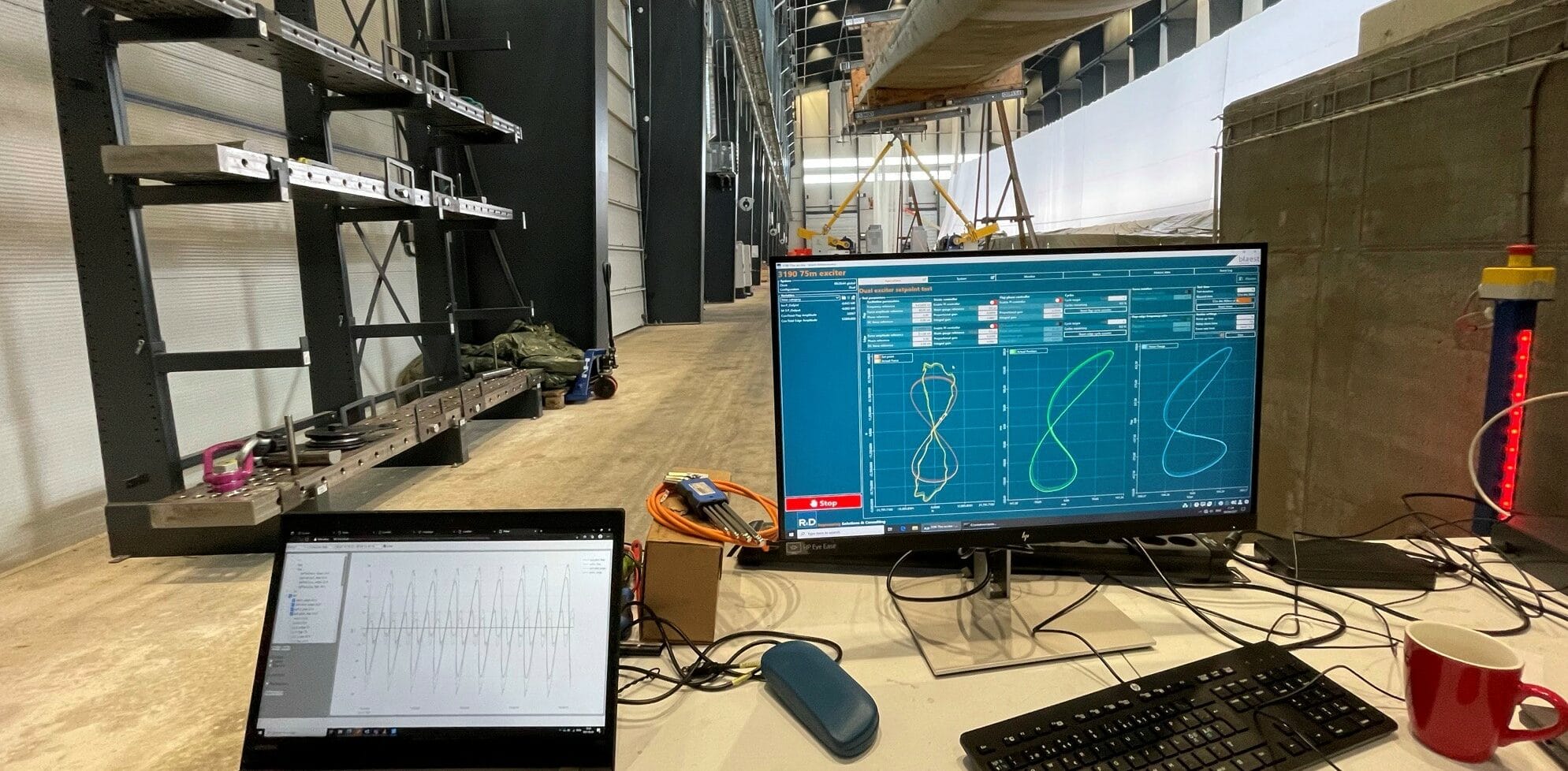
Test Systems
New test method will reduce time-to-market for large wind turbine blades
New test method will reduce time-to-market for large wind turbine blades
All new wind turbine blades must pass a range of tests before being approved for production. During this test period, the new EUDP-funded project, BLATIGUE-2, wants to shorten drastically to speed up the approval process of the blades.
"The project's vision is to create a fast, smart method to perform tests. We will develop new tools and software which the industry needs. When the tests of the blades are improved, fewer errors will occur, they will become more reliable, and this will also increase the wind energy's competitiveness," says Project Manager Kim Branner from DTU Wind.
The BLATIGUE-2 project builds on the successful and previously EUDP-funded project BLATIGUE. This project developed the multi-axis fatigue blade test system, Dual Axis Exciter. With the Dual Axis Exciter, OEMs can test their blades using only one test system, saving test time and changeover time when shifting between the test setups. Even though the BLATIGUE project offers unique fatigue testing possibilities, it has also revealed some technical challenges and possibilities. The BLATIGUE-2 project develops, e.g., a new test simulation software, which will make it possible to achieve the full potential of the already existing technologies.
"This project will transform state-of-art technologies and make it possible for manufacturers to improve their blade design faster, cheaper, and more efficient," says Rasmus Buch Andersen, Technical Product Manager at R&D Test Systems.
The project's vision is to create a fast, smart method to perform tests. We will develop new tools and software which the industry needs.
Software supports test planning and evaluation
The methods used for fatigue testing are complicated and take time to plan and design. To solve this challenge, the project partners will create and demonstrate a user-friendly solution, allowing end-users to plan, execute, and evaluate multi-axis fatigue tests better and faster with more extensive test coverage and realistic loading conditions. The new test method is expected to reduce unplanned blade repairs by an estimated 10% which is crucial in securing a stable wind turbine operation.
The combination of the blade exciter and test software makes it less complex to execute the blade tests and provides a significantly shorter test time. The shorter test time plays an important role in reducing the development time of new blade designs and time-to-market for the coming large offshore wind turbines.
The project is expected to be completed in 2025. However, the project partners are optimistic and anticipate being able to present the first results from the project by the end of 2022.
The project partners are DTU Wind and Energy Systems, R&D Test Systems, LM WIND POWER A/S, BLADE TEST CENTRE A/S, Juel+Krøyer A/S, Hottinger Brüel & Kjær A/S, Zebicon A/S, Siemens Industry Software NV, DET NORSKE VERITAS. DANMARK A/S, Olsen Wings A/S, and Ørsted Wind Power A/S.
Introduction to BLATIGUE-2
Kim Branner, Project Manager at DTU Wind.
The project will develop and demonstrate four technologies
Smart fatigue test exciter with software (R&D Test Systems A/S)
This will enable end-users to plan, execute and evaluate multi-axis fatigue tests better and faster with more comprehensive test coverage and more realistic loading conditions.
Product Data Management and digitalization (Juel+Krøyer A/S)
The data management solution and accompanying consultancy service will address a major inefficiency gap between the physics/engineering and business of companies which will lead to a faster certification process and frontloading of knowledge.
Virtual sensing technology (Hottinger Brüel & Kjær A/S)
The virtual sensing technology will significantly reduce the need for physical sensors and data acquisition channels which will reduce CAPEX for hardware and sensor investments and reduce man-hours and testing time.
Non-contact measurement hardware (Zebicon A/S)
The new measurement hardware will provide much more comprehensive data with full-field measurements instead of point measurements. It also enables reduced time for instrumenting blades for testing and reduces a current problem related to the need to replace sensors during testing.
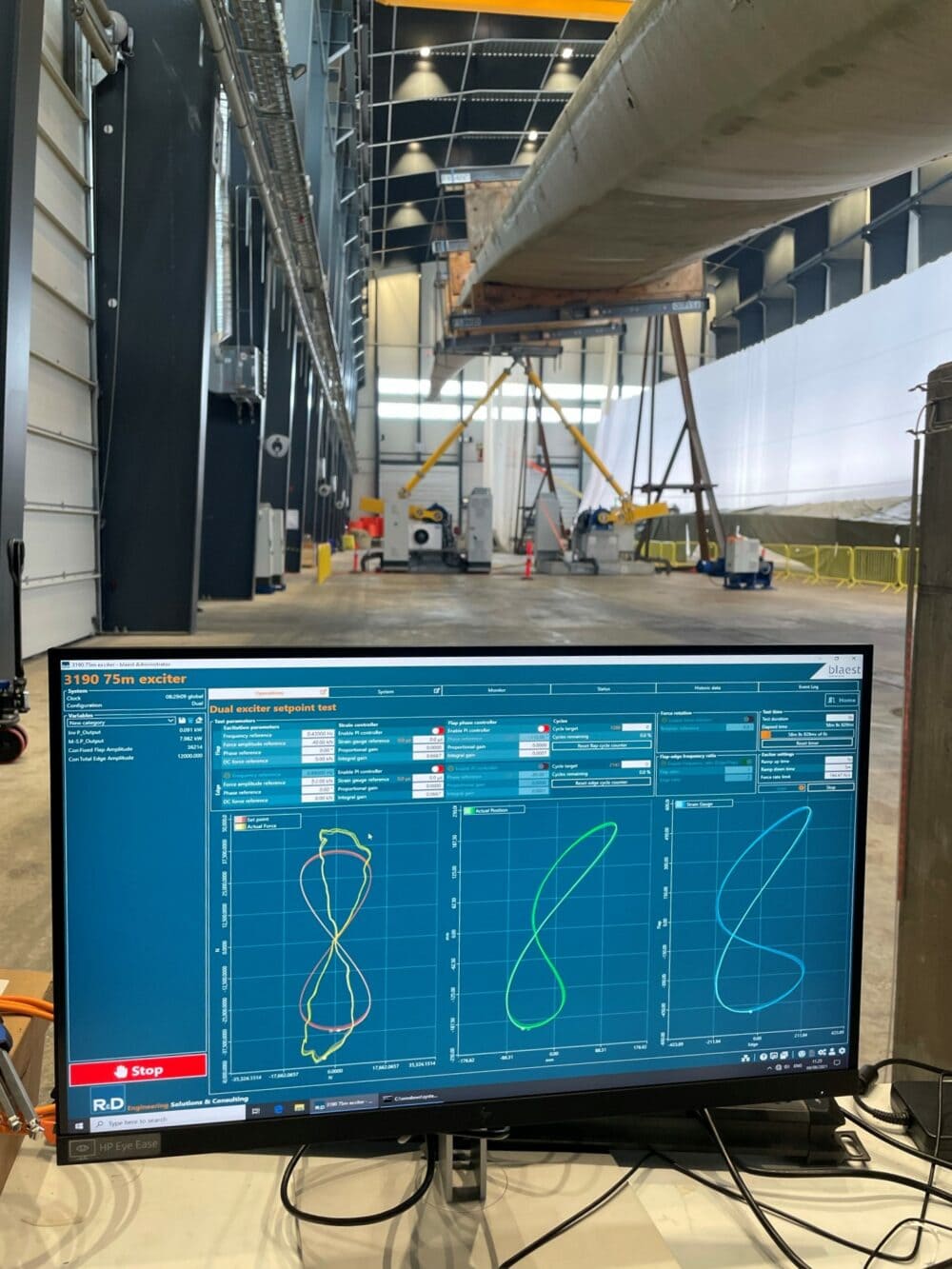