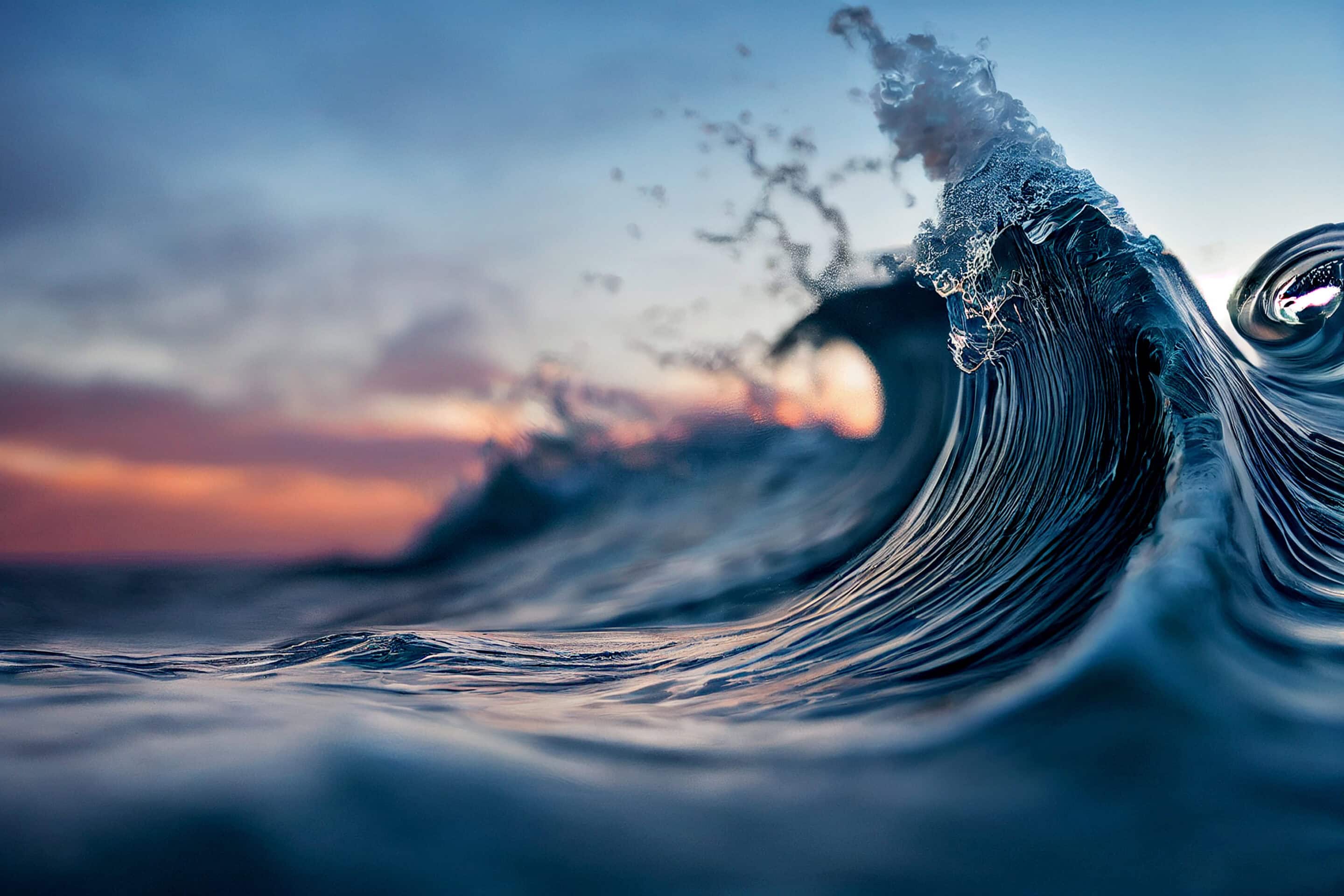
Floating Wind
Advancing Floating Wind Technology with Testing
Advancing Floating Wind Technology with Testing
Floating Wind
Offshore wind farms capture wind resources that are stronger and more consistent than those on land. However, offshore is limited by the depth of the water. That’s where floating wind technology allows turbines to be deployed in deep waters where traditional fixed-bottom structures aren’t feasible. This expands the areas where wind power can be harvested and takes advantage of stronger offshore breezes.
New conditions also mean new testing requirements—increased accelerations, loads, movements, and unseen challenges to components, subsystems, and service operations. We know the challenges, understand the technology, and have experience with failure modes and testing.
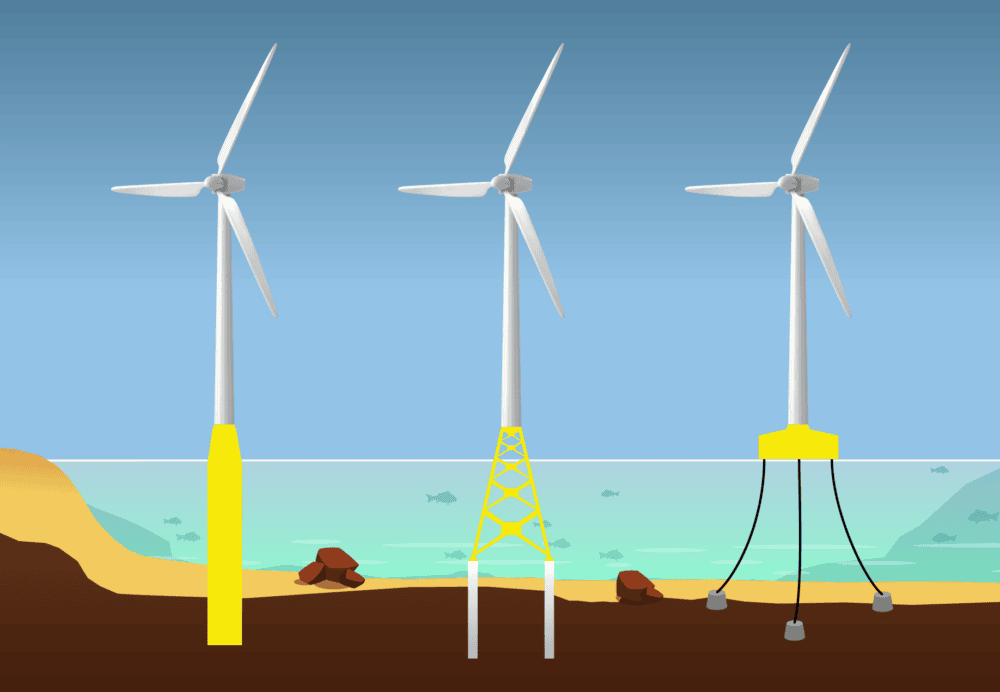
Testing Solutions
The solution calls upon new testing topologies and methods. Especially the nacelle and its sub-components on the new floating platforms will face substantial changes in loading profiles experienced during its service life. These new loading profiles cannot be verified through previous testing methods but can be mitigated through newly developed testing solutions. At R&D Test Systems, we know the challenge and the solution. We are here to guide, advise, develop, and deploy new test solutions specifically for floating wind turbines and their subcomponents.
Discover possibilities with a Feasibility Study
Discover how R&D Test Systems can elevate the potential of your floating wind projects. Connect with our experts to learn more about the possibilities to work with us on a future project, or start with a feasibility study to understand better your testing needs and the best test solution to match this.
How can we help you?
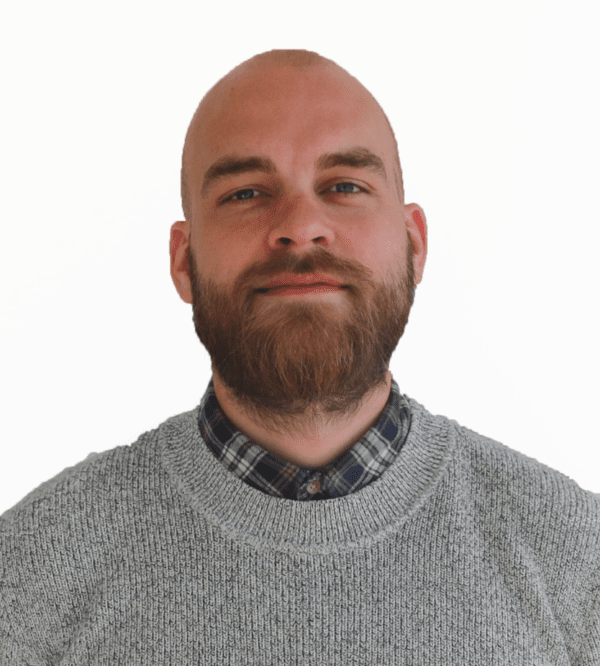
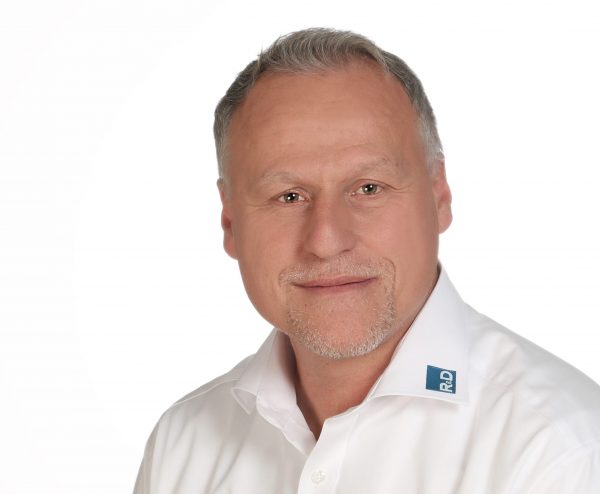
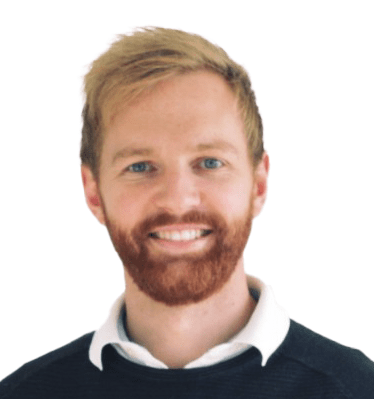