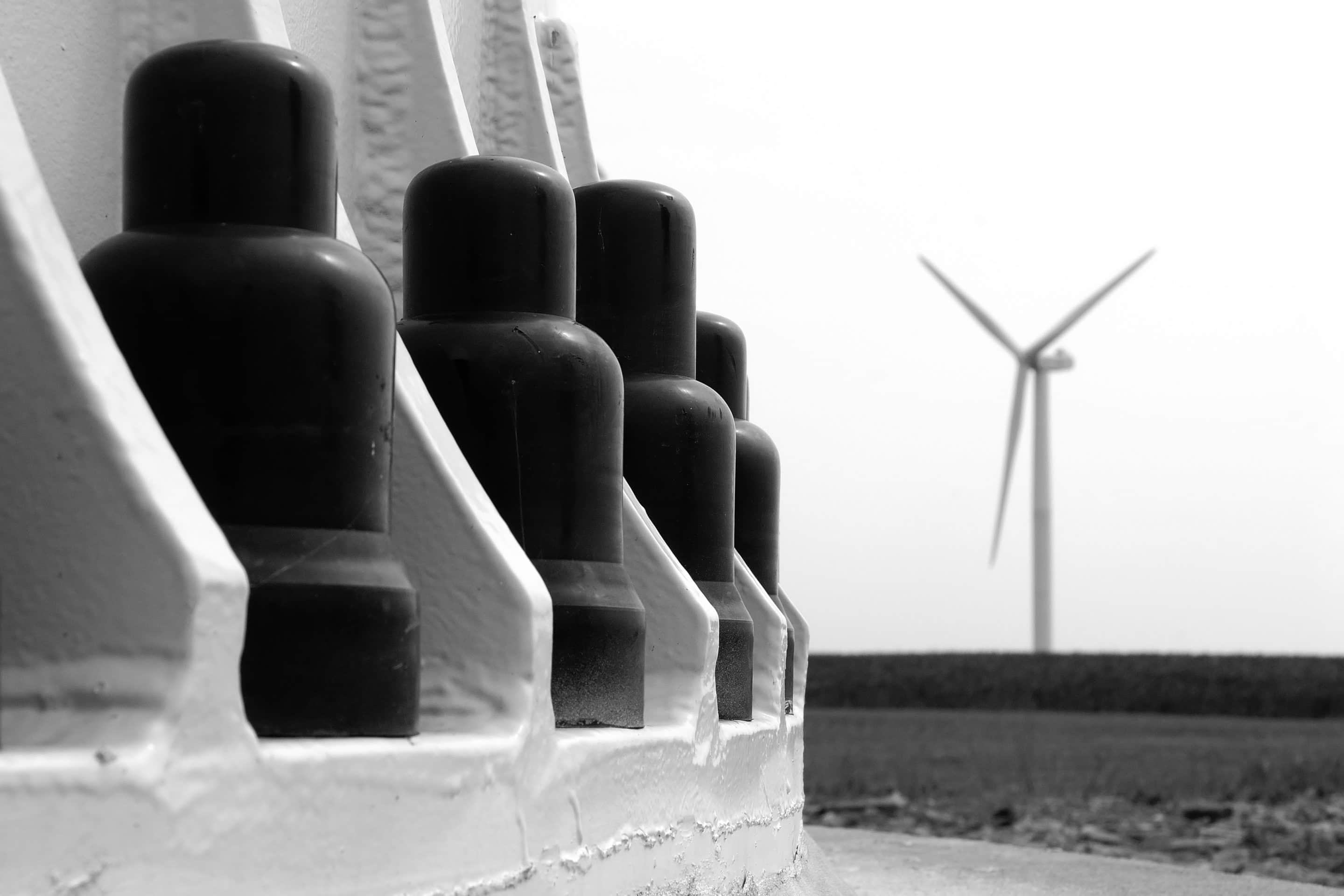
Which of the many ways to tension wind turbine bolts in service is most accurate, quickest and cost-efficient?
Which of the many ways to tension wind turbine bolts in service is most accurate, quickest and cost-efficient?
Wind turbines typically contain more than 6,000 bolts. The inspection of the larger critical bolts is required at regular intervals – these inspections are time consuming and therefore expensive, and often the results obtained can vary, depending on the actual inspection method.
Every bolted joint in a wind turbine is set to the appropriate joint loading tension during the assembly process, but it then requires regular in-service tension inspections. This is because a bolt can lose tension over time due to the forces and vibrations they are subjected to, a situation that, at worst, could result in the failure of the entire turbine.
Torque, tension, and state-of-the-art tools
This regular inspection of the bolts is carried out in line with the manufacturer’s maintenance schedule to ensure safe and optimal operation. This is usually accomplished using torque or tension tools, but recently new methods have been developed using ultrasound, load sensors, or mechanical indicators.
“There are a lot of factors to take into account when choosing the correct tool for this vital job,” says Flemming Selmer Nielsen, Senior Specialist of Danish engineering company R&D Test Systems.
“Those undertaking this monitoring work are well-advised to choose a solution that is not only quick and easy to operate, but also reliable in the long-term and available at the right price. Many of these monitoring systems require special preparation of the bolts leading to higher costs and logistical challenges,” he adds.
Bolt-tension tools increasingly use ultrasound
R&D Test Systems, an engineering company headquartered in Denmark supplying test systems and consultancy for the wind energy sector, developed the Bolt-Check system, a bolt-tension measuring tool that provides an optimal balance between user-friendliness, accuracy, reliability, and cost. Designed to be used on standard bolts, Bolt-Check offers wind turbine manufacturers and service companies a series of benefits normally only available at much higher prices.
Increasingly, bolt-tension tools use electronic sensing methods like ultrasound. The operating principle is based on using sound waves to measure the length of the bolt, which lengthens during tensioning. The tension can then be calculated. Mechanical methods for measuring bolt tension, on the other hand, typically use a caliper that mechanically measures the change in length.
One way of monitoring a bolt’s tension while it is in service is by using specially designed bolts with embedded tension indicators. These bolts will indicate a loss of tension, but the problem is they have a substantial initial investment cost.
Up to 50 times lower costs for the individual bolt
The “Bolt-Check Advanced”, a tool developed by R&D Test Systems to measure the tension of installed bolts, offers a cost-effective solution to easily determine the actual clamping force in bolts.
“This Bolt-Check system can be implemented at a cost of 3-4 Euros per bolt which represents a cost advantage for wind turbine manufacturers since alternative systems using specialized bolts can increase the cost 10 to 50 times per bolt, or even more, depending on the bolt size,” comments Selmer.
This tool does not require thousands of bolts to be loosened and then re-tensioned in order to measure the loading on the joints. Instead, it uses its proprietary method based on combining an ultrasonic length measurement with a mechanical measurement. This is done using a custom tool featuring a micro-gauge and an ultrasonic sensor which can be used to check any standard bolt.
Hundreds of bolts accurately checked within hours
Using R&D Test Systems’ patented method involving both mechanical and ultrasonic measurements along with the uniformity of properties within the different bolt batches, it is possible for Bolt-Check to achieve an accuracy of approximately 10 percent. There is also a huge time-saving advantage as the system allows hundreds of bolts to be checked in just a few hours.
“We are offering a solution that gives a high level of accuracy at a very competitive price and even more importantly, it saves a huge amount of time,” comments Selmer.
“Traditional tools are heavy and potentially dangerous as they operate at high hydraulic pressure. Bolt-Check is easy to use and hand-held, therefore, it also provides significant health, safety, and environmental improvement,” concludes Selmer.
We are offering a solution that gives a high level of accuracy at a very competitive price and even more importantly, it saves a huge amount of time