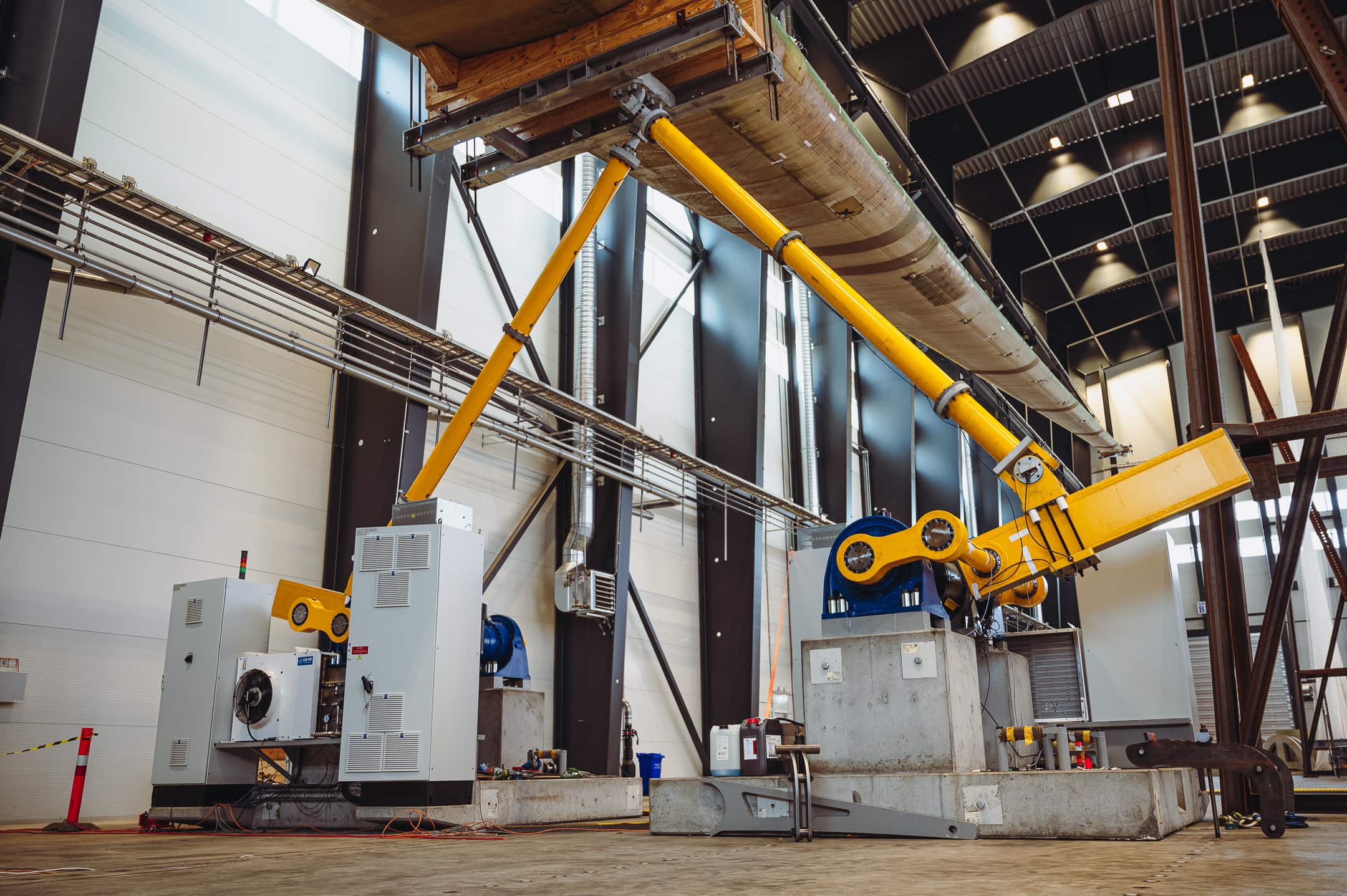
Test Systems
Offshore wind turbine testing – an investment to save millions
Offshore wind turbine testing – an investment to save millions
With specialized testing, wind turbine manufacturers can reduce time to market and identify potential weaknesses resulting in failure, downtime, and expensive repairs that can cost even more than 100,000 euros a day.
R&D Test Systems predicts that with the next generation of offshore wind turbines set to become bigger, more powerful, and having shorter development cycles, validation testing all along the wind turbine value chain will become essential as it allows manufacturers to evaluate these new products under realistic conditions, thus estimating lifespan and maintenance requirements. This process can save millions of euros in warranty claims and downtime, and at the same time, add reliability.
Although it is 30 years since Denmark, the home of R&D Test Systems, built the world’s first offshore wind farm at Vindeby, the sector remains far from mature. Offshore wind currently provides just three percent of Europe’s electricity with 25 GW of capacity, but the region targets 110 GW by 2030 with significantly more to follow. This increase in capacity will drive the trend for even more giant turbines.
To meet this imminent demand for larger and more powerful offshore wind parks, manufacturers are developing more advanced and specialized units – often with a shorter time to market – and these need to comply with a range of industry standards, some of them new.
“As an expert in developing and delivering test systems for wind turbines including nacelles, rotor blades, gearboxes, and other key components, it is our job to know what the current and upcoming standards are and to build test rigs that are flexible for other product updates. The test rigs not only encompass the new standards but also accommodate customer-specified tests,” comments Sascha Heinecke, sales director, R&D Test Systems.
“The next generation of wind turbines will need to be as reliable as possible, and planning for testing at the development and prototype stage is wise as it is an investment that has the potential to save millions of euros. By testing early, the manufacturer has the chance to improve their design sooner at minimum cost,” adds Heinecke.
Repairs at sea can easily cost 100,000€ a day
A failure scenario that occurs out at sea can take days or even weeks to solve and often requires helicopters and special ships, in addition to very scarce and often booked specialist technicians, which can typically add up to more than 100,000 euros a day. On top comes the cost of replacement parts and the loss of revenue from idle turbines.
“Testing components thoroughly is vital to mitigate manufacturer’s exposure to wind turbine downtime and warranty claims. This will become even more important as the offshore wind starts to represent a greater proportion of the collective energy mix,” says Heinecke.
Reliable operation reduces warranty claims
Increasing the number and size of wind farms is part of the current trend. “Reliable operation will grow in importance. Energy interruptions from offshore wind farms should only ever occur due to insufficient wind speed and never because of a preventable failure,” explains Heinecke.
R&D Test Systems has a team of specialists who develop and deliver turnkey test rigs for wind turbines and works with manufacturers to identify the potential cost advantages.
Testing optimizes the value chain
R&D Test Systems predicts that validation testing will become an essential part of the offshore wind value chain as the investment in testing offers future cost savings. Services, including activities to maintain products and enhance customer experience, are a key element of modern industrial value chains, and testing is an important but challenging part of this.
“There are about eight critical components that we test in the drivetrain of modern offshore wind turbines, and together they add up to about 30% of the cost of production. The rotor blades, for example, are critical components that represent a significant part of the value chain and for which we offer specialist tests, as well as for other components and complete turbines,” says Heinecke.
Business benefits from testing
Investing in testing is a significant cost factor, but a clear picture of the financial benefits equips the wind turbine manufacturers with a compelling business case for funding this part of their business.
“If carrying out a particular test can help reduce the probability of a wind turbine failing, the manufacturer can understand exactly what the investment in testing is worth and how much money can be saved,” concludes Heinecke.
R&D Test Systems’ expert offering includes its highly accelerated lifetime testing (HALT), the world’s largest test bench for full-scale nacelle testing, with wind force simulations powered by R&D’s 25 MW motor that enables manufacturers to discover weaknesses and determine failure mechanisms.
Other tests include:
- Gearbox Test Bench – for functional, end-of-line, or HALT testing of gearboxes.
- Bearing Test Bench – tailor-made test system for large-scale bearings.
- Generator Test Bench - for functional and end-of-line
- System Integration Test for various drive line components
- Dual Axis Blade Exciter – a full-scale multi-axis fatigue blade test system.
- Rain Erosion Tester – for testing wind turbine blades leading edges of wind turbine blades that meets industry standards.
- Pitch System Test Bench – tailor-made system for complete pitch systems or pitch bearings.
- Yaw Ring Test Bench – for testing of yaw ring segments.
Read more about large-scale test systems for the wind turbine industry.