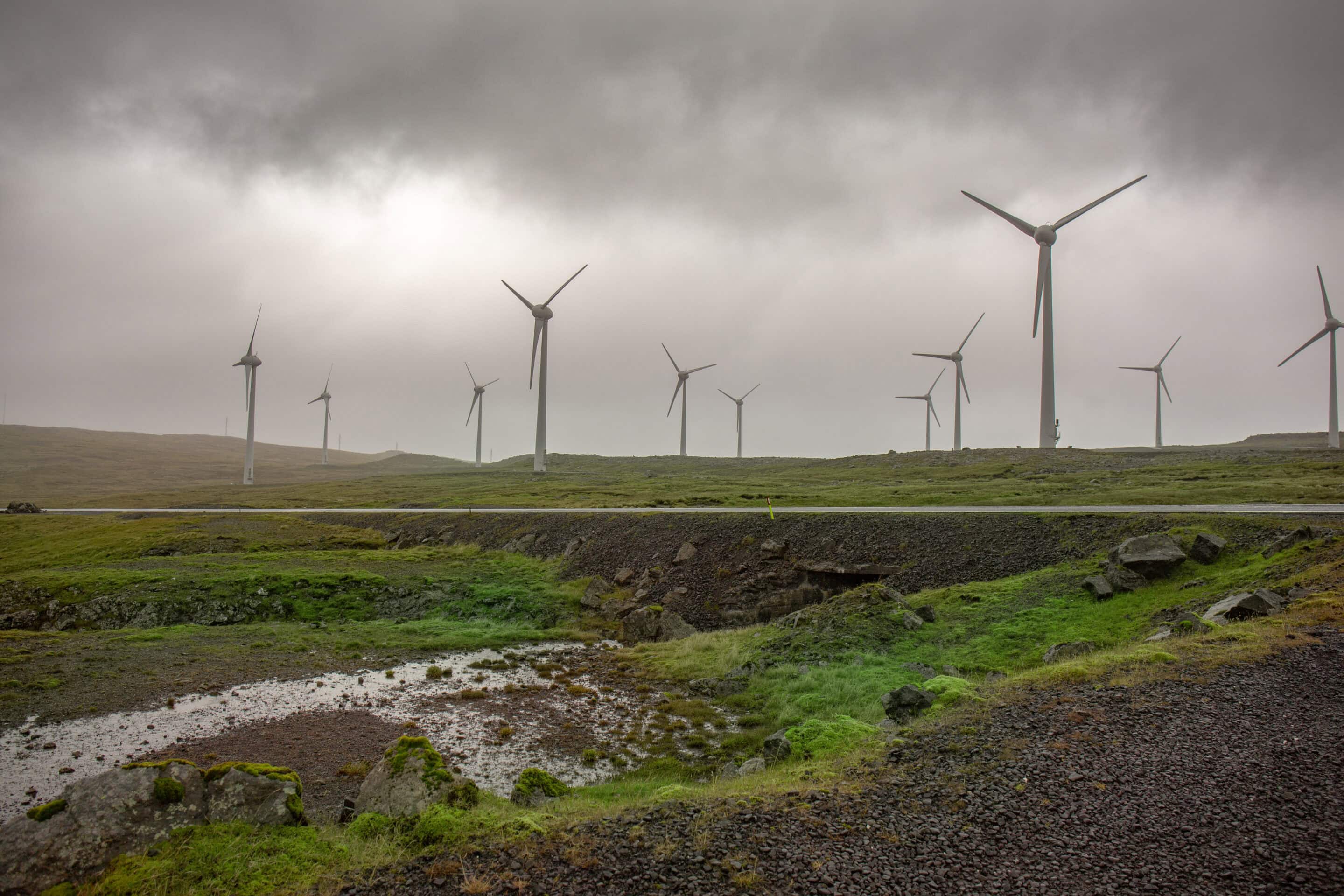
Bolt-Check
Reduction of service maintenance costs by 75% with Bolt-Check
Reduction of service maintenance costs by 75% with Bolt-Check
Heavy equipment, unpredictable weather, and remote locations make bolt tension verification time-consuming and costly. However, by integrating Bolt-Check into a maintenance routine, Mr. Eyðfinnur Lenvig has significantly reduced both time and expenses while improving the accuracy of bolt inspections.
Wind turbine foundations require periodic bolt tension checks to ensure structural integrity. Traditionally, this process required hydraulic tensioning equipment that was both heavy and difficult to transport. “Originally, the bolts were tensioned using a jack that was so heavy it needed a crane just to move it,” explains Lenvig.
When the wind farm owner needed the bolts inspected after one year, Lenvig explored alternatives. “My son, who was studying at the University of Southern Denmark at the time, introduced me to Bolt-Check after hearing about it from one of his professors,” he says. This led to a discussion with R&D Test Systems, where Lenvig learned how ultrasonic measurement could streamline the process. “After a meeting with your specialists, I presented the solution to the wind farm owner, who was interested in testing it.”
The transition to Bolt-Check began with a comparative study. “We initially tested all the bolts using the hydraulic jack and then recorded the data with Bolt-Check,” Lenvig recalls. “On one turbine, we even fully loosened each bolt one at a time to establish a reference point.” By the second year of inspections, Bolt-Check became the primary tool, eliminating the need for hydraulic equipment altogether.
Significant time and cost savings
Using Bolt-Check has led to a drastic reduction in maintenance time. “With your system, the entire process can be done in a single day by one person,” says Lenvig. “Had we continued using the hydraulic equipment, we would have only been able to test every tenth bolt, and the process would have taken at least three days.”
The cost benefits are equally compelling. “Expenses for the wind farm owner have decreased by about 75% or more,” he notes. Previously, inspections required expensive equipment rental, transportation, and additional personnel. “With the old system, we needed an electric generator, a hydraulic station, a jack, an extra technician, and a crane truck just to handle the equipment. Plus, we needed a transport vehicle for storage, as the equipment couldn’t be left on-site overnight without supervision.”
Data-driven maintenance for long-term reliability
Beyond saving time and costs, Bolt-Check provides a critical advantage: long-term data tracking. “We can now measure and document exactly how much tension the bolts lose each year,” says Lenvig. “This wasn’t possible with the hydraulic jack.”
This data-driven approach enhances predictive maintenance, helping wind farm operators ensure that bolts remain within the correct tension range, improving overall turbine reliability and lifespan.
Expanding the potential of Bolt-Check
Given its success in wind turbine maintenance, Lenvig believes Bolt-Check has applications beyond the renewable energy sector. “Any large bolts requiring precise tensioning should be checked with ultrasonic measurement,” he suggests. “It increases bolt lifespan and ensures consistent, correct tensioning.”
As Mr. Eyðfinnur Lenvig will continue to promote efficient maintenance solutions in the Faroe Islands, Bolt-Check has become an invaluable tool in their service operations. With its ability to replace cumbersome hydraulic systems, reduce costs, and provide precise data, Bolt-Check sets a new standard for bolt inspection in the wind industry and beyond.
Let’s solve your bolt tightening challenges
We offer deep technical insight, practical guidance, and solutions tailored to your specific needs.
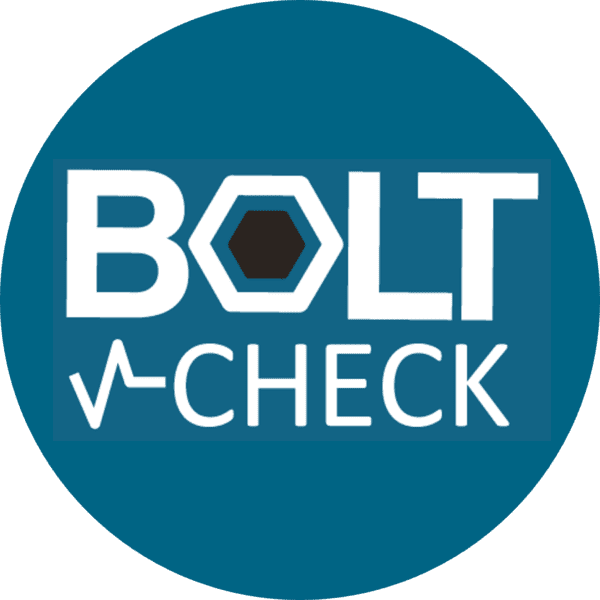