
Technology Development
R&D Test Systems supports the development of blade tools for Siemens Gamesa
R&D Test Systems supports the development of blade tools for Siemens Gamesa
For R&D Test Systems’ Senior Structural Engineer, Filip Westarp, it was a big day when he could see the project he has been working on for the last two years in action. Filip Westarp has been working as Solution Owner for the development of a new blade rack system and a blade installation yoke for Siemens Gamesa.
Overcoming challenges and futureproofing systems
It was not an easy assignment to develop the new systems as the project had to solve the challenge of moving a fully loaded blade rack with three blades from the quayside onto a barge and then offshore onto the installation vessel for the actual installation.
“Installing offshore wind turbines is extremely costly. Hence, doing this effectively without damaging any components is always a challenge. We had to figure out the best way to transition the racks between the quay and the vessels. While a blade rack would usually be sea fastened on a vessel by welding, a new, hydraulic locking system had to be developed, which would quickly and safely lock or release the sea fastening of the racks on either the barge or the installation vessel,” explains Filip Westarp.
Another challenge for the team was that the blades were turned 90 degrees compared to previous SGRE blade racks. Wind turbine blades are constantly growing in size and weight. So, to optimize the processes from blade manufacturing to installation, blades now remain in the flap-wise orientation in which they are produced.
“It’s a completely new blade rack system, and we had to consider a lot of new parameters as the blades are both getting bigger and lying flap-wise,” explains Filip Westarp.
The flapwise orientation also presented the challenge of accessing the blades below as they were stacked. To get to all the blades in the blade rag, a “fold up” system was developed that makes the clamp, in which the blade is lying, tip open to gain access to the blade lying below. Furthermore, the rack system had to be future-proof regarding the number of blades and their size. This resulted in a modular rack system that can handle 6-18 blades with a length of up to an impressive 115 meters.
New yoke system
The blade installation yoke was another system that needed a redesign to accommodate the new setup.
“As the blades are lying flap-wise in a clamp setup, it’s not possible to use a vertical C-yoke. So, we had to engineer a new type of C-yoke that can grab the blades from the side at a horizontal angle. While this is a new system for SGRE, C-yokes are not new as such. However, the design had to cover both existing and future blade sizes and fulfill numerous requirements to optimize the offshore installation of the turbine blades at high wind speeds,” explains Filip Westarp.
Filip Westarp has 15 years of experience with structural engineering and tools for the wind turbine industry. Seeing the final products being used and working as intended is always exciting.
“As much as I like the development and engineering phase, there’s nothing like seeing your hard work coming to life. It never gets old,” concludes Filip Westarp.
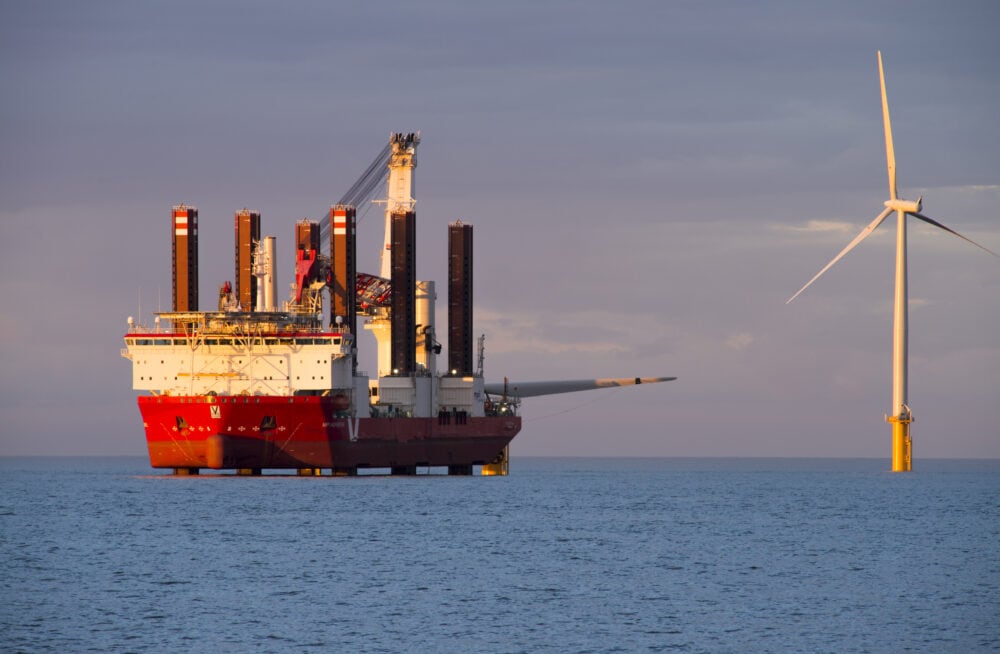
About the project
The new installation setup is being used at the new South Fork Wind project in the US, which started the installation in November 2023. The project required pre-assembled tower sections, a nacelle, and three blades to be loaded onto a transport barge that is being pulled to the offshore site, where all components are lifted onboard an installation ship which does the final installation of the offshore wind turbine 35 miles off Montauk, New York.
See a picture of the new blade rack system here and pictures of the new blade installation yoke here from the installation of the first wind turbine.
How can we help you?
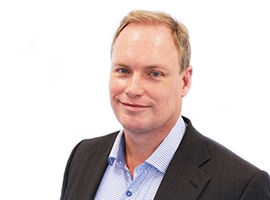