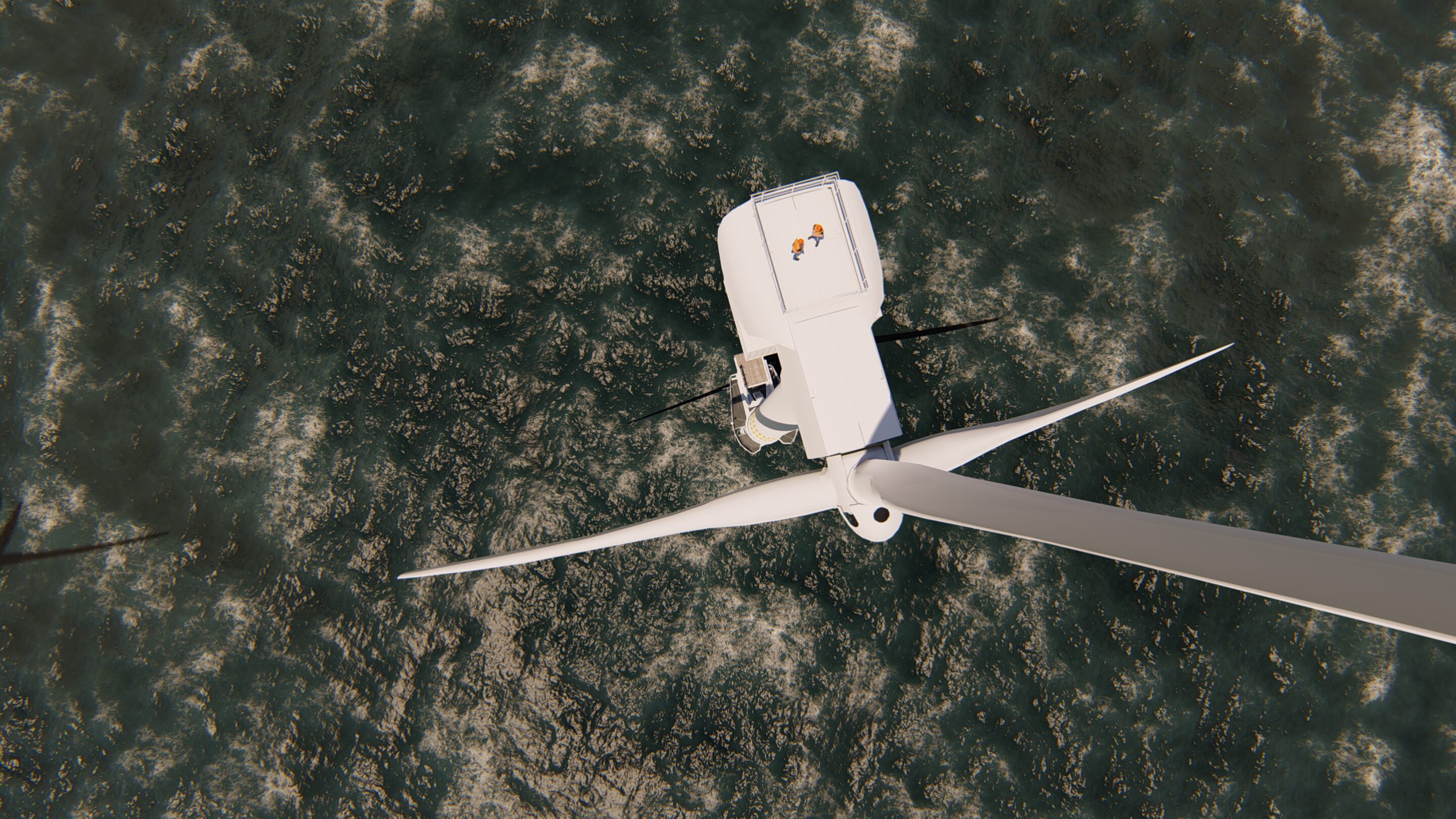
mh2 offshore optimizes offshore maintenance with Bolt-Check
mh2 offshore optimizes offshore maintenance with Bolt-Check
mh2 offshore (mh2), a specialized offshore service provider, is responsible for inspecting and maintaining critical components on wind turbines, including bolted flange connections. By integrating Bolt-Check into their workflow, mh2 has improved efficiency and accuracy in assessing bolt tension, reducing the need for time-consuming manual checks.
mh2 conducts annual inspections of offshore wind turbines, including non-destructive testing of bolted flange connections. Before adopting Bolt-Check, these checks required manual ultrasonic measurements using separate equipment, a process that was both time-intensive and complex.
“The customer we’re working with used to rely on a different ultrasonic system, but it was complicated to use, especially with changing personnel,” explains Pascal Rothstein from mh2. “Now, with the RFID integration in Bolt-Check, the process is much easier and faster.”
By storing historic measurement data directly in the Bolt-Check system, mh2 technicians can quickly verify bolt tension without manually referencing past records. “With Bolt-Check, you don’t have to reposition the transducer manually each time—you instantly know if something is off. It saves us a lot of time in the tower,” Rothstein says.
Increased efficiency and accuracy
A typical offshore wind turbine features > 130 bolts in a single flange connection, making the inspection process demanding. “Before, measuring every bolt manually was a tedious task. Now, with the RFID tags and Bolt-Check’s simplified interface, we can complete inspections much faster,” Rothstein explains.
The system provides a direct and precise reflection of bolt elongation and tension. “You see the curves move in real time as you tighten a bolt. It gives an accurate insight into stress and elongation,” he says.
Unlike traditional torque-based tightening methods, which rely on indirect force estimation, Bolt-Check allows mh2 to measure actual bolt tension without needing to reapply force. “The biggest advantage is that we don’t have to touch the bolt to check its condition. Applying force can alter the bolt’s behavior, but with Bolt-Check, we get precise readings without interference,” Rothstein states.
A smarter alternative to traditional retightening
Bolt-Check also enables mh2 to move away from conventional torque-based retightening methods, which require extensive equipment. “For smaller bolts, we still use torque wrenches, but for large-diameter bolts like M72 in wind turbine flange connections, we rely on Bolt-Check,” says Rothstein. “Instead of bringing heavy hydraulic torque tools offshore, we can perform tension verification with a lightweight, handheld device.”
Traditional methods often require engineers to mark bolts and monitor movement over time. With Bolt-Check, this process is replaced by precise ultrasonic readings. “You just check the existing forces in the bolts and determine if action is needed,” Rothstein explains. “It’s much more efficient and eliminates unnecessary intervention.”
Expanding Bolt-Check’s potential
While mh2 primarily operates in the wind industry, Rothstein sees potential for Bolt-Check in other sectors. “Any industry using pre-tensioned bolted connections could benefit from this system,” he says. “For bolts M36 and above, Bolt-Check eliminates the need for large-scale retightening equipment and simplifies verification.”
Through its use of Bolt-Check, mh2 has optimized offshore wind turbine maintenance, reducing inspection time while improving measurement accuracy. As industries continue to seek reliable and cost-effective bolted joint monitoring solutions, Bolt-Check is proving to be a game-changer in ensuring structural integrity with minimal operational disruption.
Let’s solve your bolt tightening challenges
We offer deep technical insight, practical guidance, and solutions tailored to your specific needs.
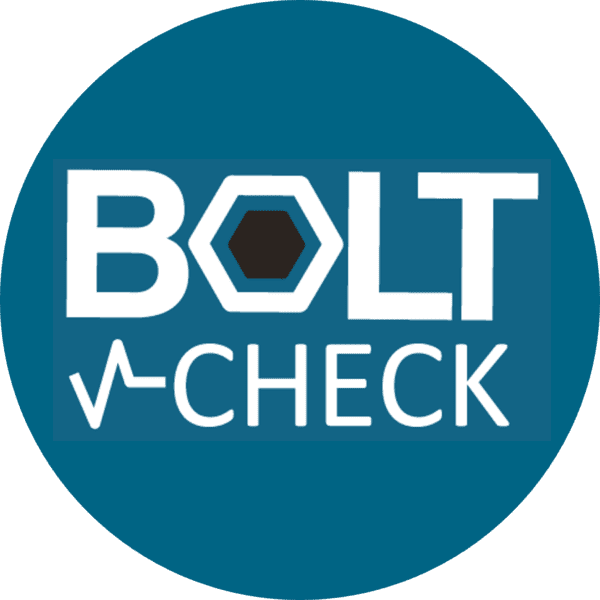