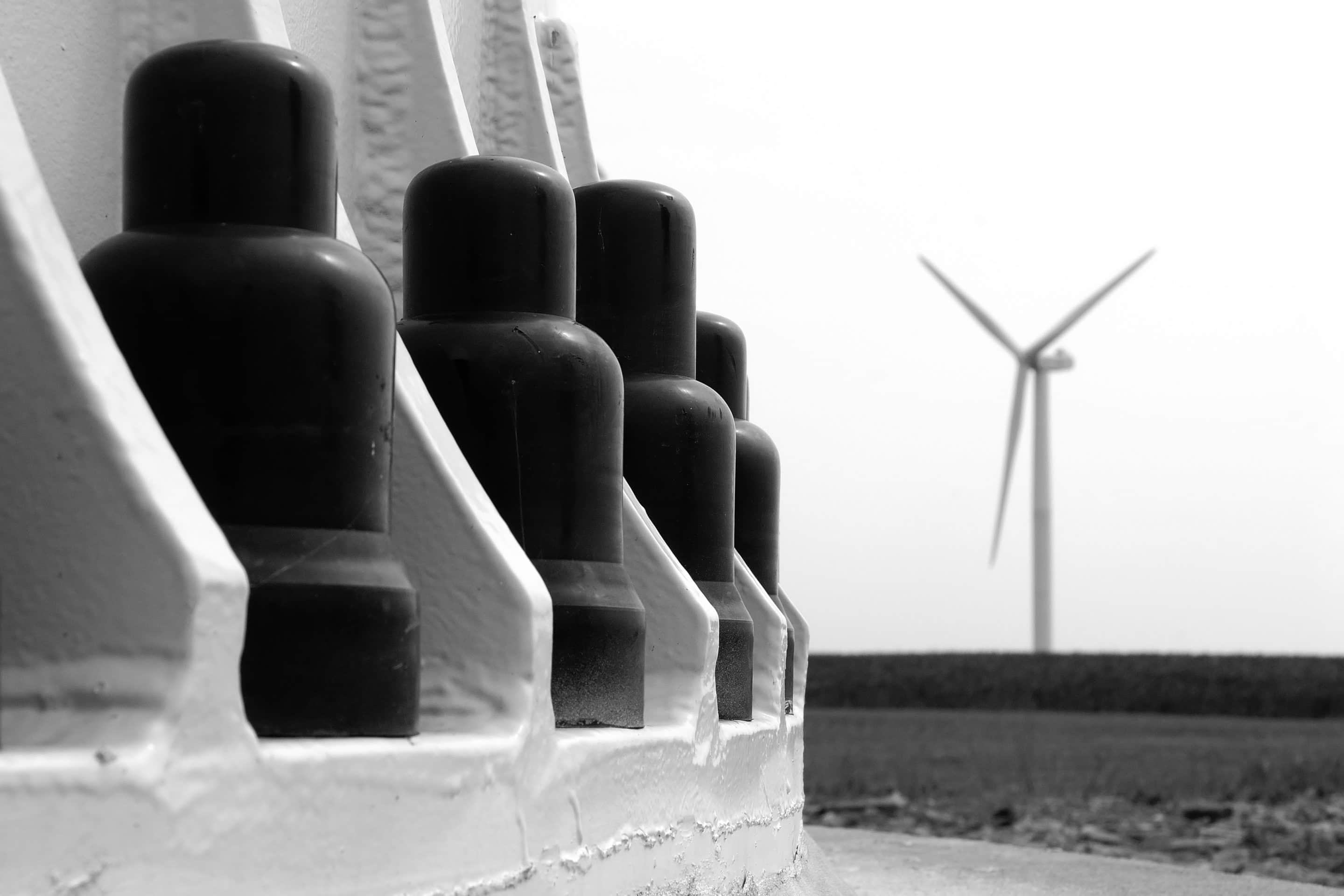
Wartung von Bolzen in Windkraftanlagen: Welche Methode ist schnell, genau und kosteneffizient?
Wartung von Bolzen in Windkraftanlagen: Welche Methode ist schnell, genau und kosteneffizient?
Windkraftanlagen enthalten üblicherweise mehr als 6.000 Schrauben. Die Prüfung der größeren kritischen Bolzen ist in regelmäßigen Abständen erforderlich. Diese Wartung ist zeitaufwendig und daher teuer, und oft können die erzielten Ergebnisse je nach Prüfmethode variieren.
Jede Schraubverbindung in einer Windkraftanlage wird während des Montageprozesses mit dem passenden Anzugsdrehmoment vorgespannt, erfordert dann aber regelmäßige Spannungsprüfungen während des Betriebs. Denn ein Bolzen kann im Laufe der Zeit aufgrund von Kräften und Vibrationen, denen er ausgesetzt ist, an Spannung verlieren: Eine Situation, die im schlimmsten Fall zum Ausfall der gesamten Turbine führen kann.
Drehmoment, Spannung und modernste Werkzeuge
Diese regelmäßige Überprüfung der Bolzen wird gemäß dem Wartungsplan des Herstellers durchgeführt, um einen sicheren und optimalen Betrieb zu gewährleisten. Dies wurde bislang mit Drehmoment- oder Spannungswerkzeugen durchgeführt. Mittlerweile sind aber neue Methoden entwickelt, die Ultraschall, Lastsensoren oder mechanische Indikatoren verwenden.
"Es gibt viele Faktoren, die bei der Wahl des richtigen Werkzeugs für diese wichtige Aufgabe zu berücksichtigen sind", sagt Flemming Selmer Nielsen, Senior Specialist des dänischen Entwicklungs-Dienstleisters R&D Test Systems.
"Wer diese Überwachung übernimmt, ist gut beraten, eine Lösung zu wählen, die nicht nur schnell und einfach zu bedienen ist, sondern auch langfristig zuverlässig ist und zu einem angemessenen Preis-Leistungs-Verhältnis verfügbar. Viele dieser Prüfwerkzeuge erfordern eine spezielle Vorbereitung der Bolzen, was zu höheren Kosten und logistischen Herausforderungen führt", fügt er hinzu.
Bolzenvorspannungs-Messgeräte verwenden zunehmend Ultraschall
R&D Test Systems, ein Ingenieur-Dienstleister mit Hauptsitz in Dänemark, der Prüfsysteme und Beratung für den Windenergie-Sektor anbietet, hat das Bolt-Check-System entwickelt: Ein Bolzenvorpannungs-Messgerät, das ein ausgewogenes Verhältnis von Benutzerfreundlichkeit, Genauigkeit, Zuverlässigkeit und Kosten bietet. Bolt-Check ist für den Einsatz an Standardschrauben konzipiert und bietet Herstellern von Windkraftanlagen und Serviceunternehmen eine Reihe von Vorteilen, die normalerweise nur zu wesentlich höheren Preisen erhältlich sind.
Bolzenvorspannungs-Messgeräte verwenden zunehmend elektronische Sensorik wie Ultraschall. Das Funktionsprinzip basiert auf der Verwendung von Schallwellen, um die Länge der Schraube zu messen, die sich während des Anziehens verlängert. Damit kann dann die Spannung berechnet werden. Mechanische Methoden zur Messung der Schraubenspannung hingegen verwenden typischerweise einen Messschieber, der die Längenänderung mechanisch misst.
Eine Möglichkeit, die Spannung eines Bolzens während des Betriebs zu überwachen, ist die Verwendung von speziell gefertigten Bolzen mit eingebetteten Spannungsindikatoren. Diese Bolzen zeigen einen Spannungsverlust an, aber das Problem ist, dass sie mit erheblichen höheren Einstiegsinvestitionen verbunden sind.
Bis zu 50-mal geringere Kosten für die einzelne Bolzen
Der "Bolt-Check Advanced", ein von R&D Test Systems entwickeltes Werkzeug zur Messung der Spannung von installierten Bolzen, bietet eine kostengünstige Lösung zur einfachen Bestimmung der tatsächlichen Spannkraft in Bolzen.
"Dieses Bolt-Check-System kann zu Kosten von drei bis vier Euro pro Schraube implementiert werden, was einen Kostenvorteil für die Hersteller von Windkraftanlagen darstellt, da alternative Systeme, die spezielle Schrauben verwenden, die Kosten pro Bolzen um das 10- bis 50-fache oder sogar noch mehr erhöhen können, abhängig von der Bolzengröße", kommentiert Selmer Nielsen.
Das Bolt-Check erfordert nicht, dass Tausende von Schrauben gelöst und wieder angezogen werden müssen, um die Belastung der Verbindungen zu messen. Stattdessen kombiniert es eine Ultraschall-Längenmessung mit einer mechanischen Messung. Dies geschieht mit einem Werkzeug, das mit einer Mikrolehre und einem Ultraschallsensor ausgestattet ist und mit dem jede Standardschraube überprüft werden kann.
Hunderte von Bolzen innerhalb von Stunden genau geprüft
Mit der von R&D Test Systems patentierten Methode, die sowohl mechanische als auch Ultraschallmessungen nutzt, und den ausgewiesenen Materialeigenschaften innerhalb der verschiedenen Bolzenchargen, erreicht Bolt-Check eine Genauigkeit von etwa 10 Prozent. Hinzu kommt eine enorme Zeitersparnis, da mit dem System Hunderte von Bolzen in nur wenigen Stunden geprüft werden können.
"Wir bieten eine Lösung an, die ein hohes Maß an Genauigkeit zu einem sehr wettbewerbsfähigen Preis bietet und, was noch wichtiger ist, eine enorme Zeitersparnis mit sich bringt", kommentiert Selmer Nielsen.
"Herkömmliche Werkzeuge sind schwer und potenziell gefährlich, da sie mit hohem Hydraulikdruck arbeiten. Bolt-Check ist als Handgerät einfach zu bedienen, daher bietet es auch eine erhebliche Verbesserung in den Bereichen Gesundheitsschutz und Arbeitssicherheit sowie Umweltschutz", schließt Selmer Nielsen.
Wir bieten eine Lösung an, die ein hohes Maß an Genauigkeit zu einem sehr wettbewerbsfähigen Preis bietet und, was noch wichtiger ist, eine enorme Zeitersparnis mit sich bringt